Faltmembrane
Faltbare Membrane
Für eine Hotelanlage in Kasachstan konstruierte Planex eine auf- und zufahrbare Faltmembrane.
Faltbare Membrane für Glaskuppel mit 470 m² Fläche
Für eine Hotelanlage in Almaty / Kasachstan fertigte Planex im Auftrag und nach Planung von Alfred Rein Ingenieure eine auf- und zufahrbare Faltmembrane. Im auseinandergefalteten Zustand passt sich die halbkugelförmige Faltmembrane perfekt an die Form der Glaskuppel an. Zusammengefaltet nimmt die Membrane nur wenig Platz ein.
Der Raum unterhalb der Glaskuppel ist ein Veranstaltungsraum. Das akustisch wirksame Material der Faltmembran sorgt für eine gute Raumakustik. Durch den Fahrmechanismus kann jederzeit eine fast vollständige Verdunkelung des Innenraums per Knopfdruck erreicht werden.
Technische Informationen
An freistehenden Stützmasten sind kardanisch verstellbare Metallkonstruktionen befestigt, die mit durchsichtigen Halbschalen verblendet sind. Die Halbschalen sind stufenlos in Höhe und Neigung in allen Richtungen verstellbar. Farblich gestaltete textile Wechselhüllen erfüllen die Designvorgaben.
Die Unterkonstruktion besteht aus einem Äquatorring mit kardanischer Führung sowie aus zwei durchsichtigen, demontierbaren Kunststoffhalbschalen. Am Äquatorring sind die Innenleuchten und die Halbschalen befestigt. Die textilen Wechselhüllen umschließen glatt gespannt den Leuchtkörper. Die unterschiedlich großen Leuchtkörper und die Stützmasten sind statisch überprüft.
Anforderung
Im Juli 2009 wurde bei Planex ein akustisch wirksames textiles Material angefragt, das gleichzeitig auch als Sonnenschutz einsetzbar sein sollte. Zusätzliche Anforderungen waren sehr gute Falteigenschaften und eine optisch einwandfreie Beschaffenheit für den Einsatz im Innenbereich.
Eckdaten des Projekts
Die Anforderung bestand darin, eine Innenmembran für die Glaskuppel eines Hotels in Kasachstan zu erstellen. Das Ziel war, eine Veranstaltungshalle im Sommer zu beschatten, für Events zu verdunkeln und für eine gute Akustik zu sorgen. Eine 470 m² große Fläche musste absolut passgenau konfektioniert werden, so dass im gespannten Zustand eine halbkugelige Form entsteht. Die textile Membran musste mit Anschlüssen für den Fahrmechanismus ausgestattet werden und der Dauerbelastung durch auf- und zufahren Stand halten.
Hohe Anforderungen an das Material
Um ein geeignetes Material zu finden, führte das Deutsche Institut für Textil- und Faserforschung im Auftrag von Planex einen Dauerknickversuch nach DIN 53359 durch. Über das Laboratorium Blum wurden notwendige Biaxial-Zugversuche zur Prüfung der Festigkeit des Materials und der Verbindungsnähte durchgeführt. Das Ergebnis war einwandfrei. Der Test zur Ermittlung des biaxialen Kraft-Dehnungsverhaltens und die Ermittlung des Relaxationsverhaltens blieben ebenfalls ohne Beanstandung.
Die Umsetzung – eine Herausforderung für Mensch und Maschine
Zeichnungen, Zuschnitts- und Detailpläne wurden mit der Fertigung detailliert aufbereitet. Die Art des Zuschnitts, Nahtzugaben, funktionale und technische Aspekte der Verarbeitung wurden festgelegt. Die Membransegmente wurden auf Basis von Zeichnungen im dwg-Format von einem automatisiert gesteuerten Cutter zugeschnitten, um die exakte Passform zu garantieren. Die Schweißnähte wurden in Hochfrequenztechnik verarbeitet, um extrem belastbare Verbindungen zu gewährleisten. Für die radial verlaufenden Gurte wurden Taschen eingearbeitet, um das Gewebe vor UV-Strahlung zu schützen.
Der Projektablauf – schnell und termingerecht
Zwischen der Vertragsunterzeichnung und der Fertigstellung der Faltmembran lagen nur knapp fünf Monate. Materialeinkauf, Materialtests, Abstimmung mit Lieferanten, Planern und die Fertigung im eigenen Haus wurden bei Planex koordiniert. Die termingerechte Auslieferung erfolgte im Juni 2010.
Die Generalplanung/Generalunternehmer übernahmen Alfred Rein Ingenieure
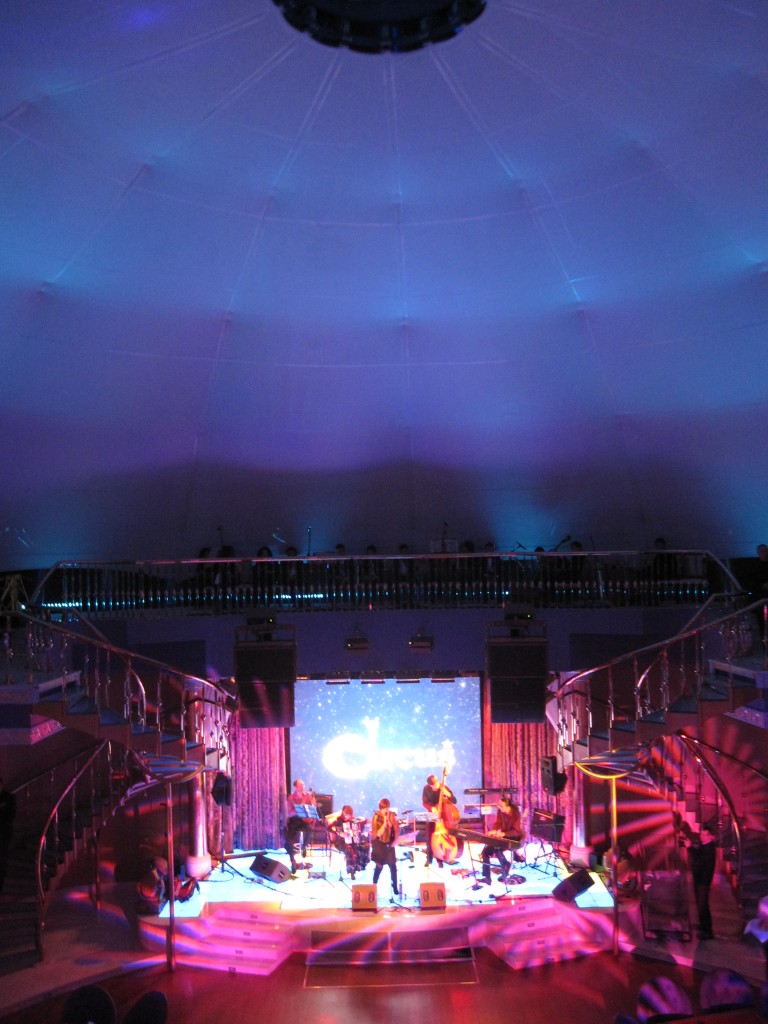
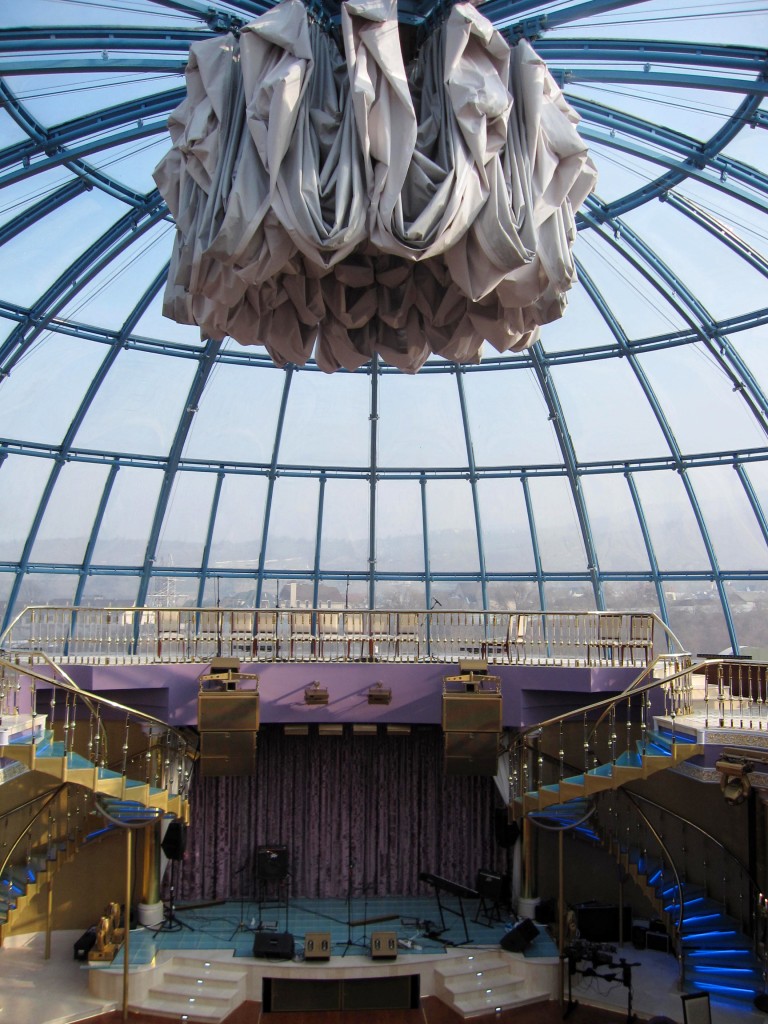
Weitere Projekte
SIE HABEN FRAGEN?
Nehmen Sie mit uns Kontakt auf.
SIE HABEN FRAGEN?
Nehmen Sie mit uns Kontakt auf.